10 Easy Steps to Remove a Rusty Bolt
- Share
- Issue Time
- Aug 3,2022
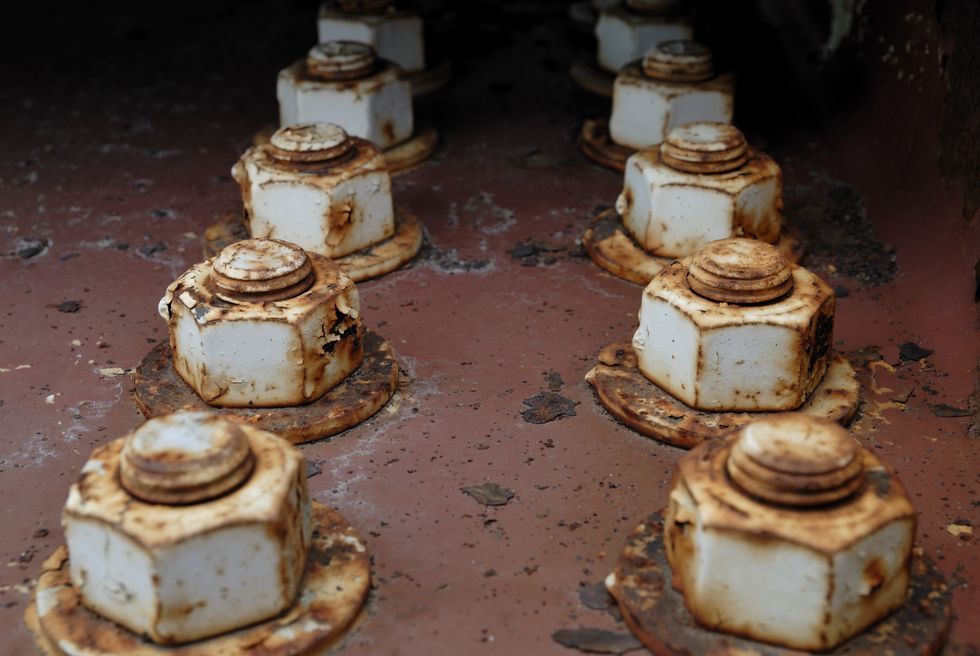
10 steps to Remove a Rusty Bolt
Removing a rusty bolt is simple, but takes some time. No worries—we'll walk you through itWe've all come across a nut that, over time, has rusted itself solid to the accompanying bolt. Removing a rusty bolt is tough, but not impossible. With a little patience, any DIY-er can tackle the challenge.
One of the most important things to keep in mind as you're working is to resist the temptation of using excessive force. This could cause you to break a blind stud, which could mean hours of drilling out the busted shank. As with all projects, assess the situation and plan carefully using the following tips and tricks.
Step 1: Check if the bolt is ready to break
The first thing you need to do is decide if the bolt is ready to break. Once a bolt yields, (stretched beyond its elastic limit), breaking is imminent. For example, exhaust manifold studs are notorious for corroding the shanks thin as twigs, and are just as easy to break.
Is the bolt actually rusted or does it have locking compound? Many factory bolts have thread locker applied. This can be softened with heat.
Is the bolt worth saving? A rusted fastener that has lost its tensile strength won't have the necessary clamping force to do its job. It may be easier to just break the bolt and replace it. Smaller fasteners ,such as body bolts and screws, often can't be saved. Use locking pliers on J-nuts so they won't spin and simply break the bolt and discard.
Step 2: Remove as much rust as possible
If the bolt is deemed salvageable, remove as much rust off the threads as possible. A stiff wire brush and a little elbow grease goes a long way toward happy results. Rust should be removed from the root of the thread, all the way to the end, so the nut doesn't gall and seize as it turns.
Step 3: Select the proper tool
Select the proper tool. Open-end wrenches are most likely to round off the flats of a stuck nut. A six-point box end is preferable to a 12-point for the same reason. If the nut is smaller due to corrosion, you may get a better fit with the next smaller metric or SAE size. For example, a ½-inch socket (12.7 millimeters) may be a better fit on rusted 13-millimeter nut. Be careful; filing of the flats can fine-tune the fit. Cut the nuts off exhaust fasteners with an abrasive wheel mounted on a die grinder.
Step 4: Remember righty-tighty, lefty-loosey
Are you turning it the correct way? Most mechanics learn the rhyme "Righty-Tighty, Lefty-Loosey" on day one, but you'd be surprised at how many still get their spatial directions confused when working in a reversed or upside-down position. Note: Most threads are left-hand loosen, but some ring gear bolts, and old '60s Chrysler lug nuts, can be backward.
Step 5: Use liquid thread-looseners
On stuck rusted nuts and bolts that can't be cut or destroyed, some type of liquid thread loosener will be a huge help. There are many different brands to choose from, but in most cases, testing has shown penetrating oil can reduce the torque required to overcome the rust bond by up to half or more. A home-brew concoction of 50 percent Acetone and 50 percent automatic transmission fluid may work well in some cases, but be mindful of the fumes.
Step 6: Soak the threads
Liberally soak the threads with penetrating oil. Whatever brand you use, you may need to repeat applications and possibly soak overnight. Remember, patience is key—it can save you hours spent drilling out a broken bolt.
Step 7: Get more leverage
A breaker bar or long-handled ratchet will give more leverage. Use steady, even pressure, paying close attention to the feel for each turn. If the tension suddenly becomes soft or rubbery, you are either breaking the bolt or stripping the threads. Wear padded mechanic's gloves to reduce skinned knuckles and the number of quarters put in the swearing jar.
Step 8: Try using heat—it can be very effective
If the nut is bonded to the bolt, you will need more serious techniques. Heat, carefully applied to one side of the nut, can expand it sufficiently to break the rust bond or melt locking compound. Be sure to first clean off all the penetrating oil and only use open flame in areas safe to do so.
Many modern cars have extensive amounts of plastic that can melt and catch fire if you are not vigilant. Because your vision is narrow through dark, tinted safety glasses, have a spotter watching for telltale smoke or flames. Fireproof welder's blankets can be used to protect vital parts and paint from flame.
I prefer using a very small oxyacetylene tip to concentrate heat in a tight area, but an inexpensive hardware store hand-held propane torch can suffice if you have the room.
Step 9: Use paraffin as a lubricant
My favorite trick for removing rusted NPT pipe plugs from cast iron is to heat the surrounding iron, then melt a candle on the threads. Paraffin will wick into the threads and act as a lubricant. Be sure to use a snug-fitting, proper-sized socket. In this example, I used a special female square drive socket that fits the square on the pipe plug.
Step 10: Use drastic measures if all else fails
A pneumatic or electric impact gun should be the tool of last resort because it often simply breaks the bolt. Use the proper impact socket, and wear gloves and safety glasses. Since these tools can be quite powerful, save them for larger nuts. If possible, use the impact on the nut side and hold the bolt with a wrench.